RAW EARTH
Re-imagining Traditional Constructions Techniques for a Contemporary Crisis
Special thanks to Alexis Yanez, Jose Moreno, Lucia Garzon, Dario Jaramillo, Marcel Blondet, Jorge Larrea, Minga Valpo and Surtierra Arquitectura.
The initial impulse to do this research was driven by a crisis in my home country, Venezuela. Even among wealthier and middle class Venezuelans, hyperinflation and scarcity have made it virtually impossible to build with conventional materials. The resulting housing shortage and dormant capital has Venezuelans of all economic circumstances scrambling for solutions.
Before I could decide how these technologies might fit into the venezuelan context, I needed to explore the precedents and present status of earth architecture in South America. It is a universal component the built environment: city centers, colonial towns, sprawling villas, adobe squats and abandoned ruins dating back thousands of years before the Europeans. Are these merely crumbling anachronisms, or do these technologies present a solution for Venezuela’s crisis? Outside of Venezuela, does earth architecture exceed expectations of contemporary standards of living, safety and durability? And what about industrialization, commercialization and the rigorous aesthetic demands of modern architecture?
In my research, I discovered that there is incredible innovation taking place in and around the community of earth architecture. There is a multinational push to formalize practices that have for centuries been the proficiency of experienced artisans. Mis Van der Rohe once wrote, “So long as we use essentially the same materials, the character of building will not change”. At this moment, earth is a novel material, engendering a space for architects to creatively explore and innovate.
My goal is to show that Earth Architecture does indeed pass muster before the standards and rigor of contemporary living and modern aesthetics. I do not mean to suggest that earth architecture is the only material of the future but to show that it is a viable and defensible alternative to what we consider conventional materials. As the architects at Surtierra said, “In fifty years, I want to be able to talk about design and I hope the fact that we are using earth as a material is not even a subject of the conversation”. That is, Earth itself should become a conventional material.



In Chacanta, Merida we studied traditional rammed earth and built a wall under the direction of Alexis Yanez
Adobe + BTC
(Earth Block)
Adobe and BTC are the most commonly used raw earth techniques. In Peru, for example, 40% of the population lives in traditional adobe structures. Adobe is made by placing a mixture of earth, water and organic material (straw or dung) into a mold. The resulting “brick” is then allowed to dry for at least three days. BTC (the spanish acronym for “compressed earth block”) is a modernized version of adobe that typically, does not contain organic material. It is made using a mechanical press (see depiction of Cinva Ram) that ensures uniformity. BTC requires little curing time.
The production process is simple, the finished product is easy to transport, and traditional construction does not require specialized skill. As a consequence, the quality of the bricks is highly variable and many adobe structures are improvised with minimal technical knowledge. In the event of a major earthquake, the collapse of these unreinforced, informal adobe structures are often responsible for many of the fatalities. The problem is not the material but the lack of technical knowledge on behalf of the brick’s producer and home’s contractor. There are inexpensive and easily implemented techniques to reinforce adobe structures and ensure the quality of the bricks.


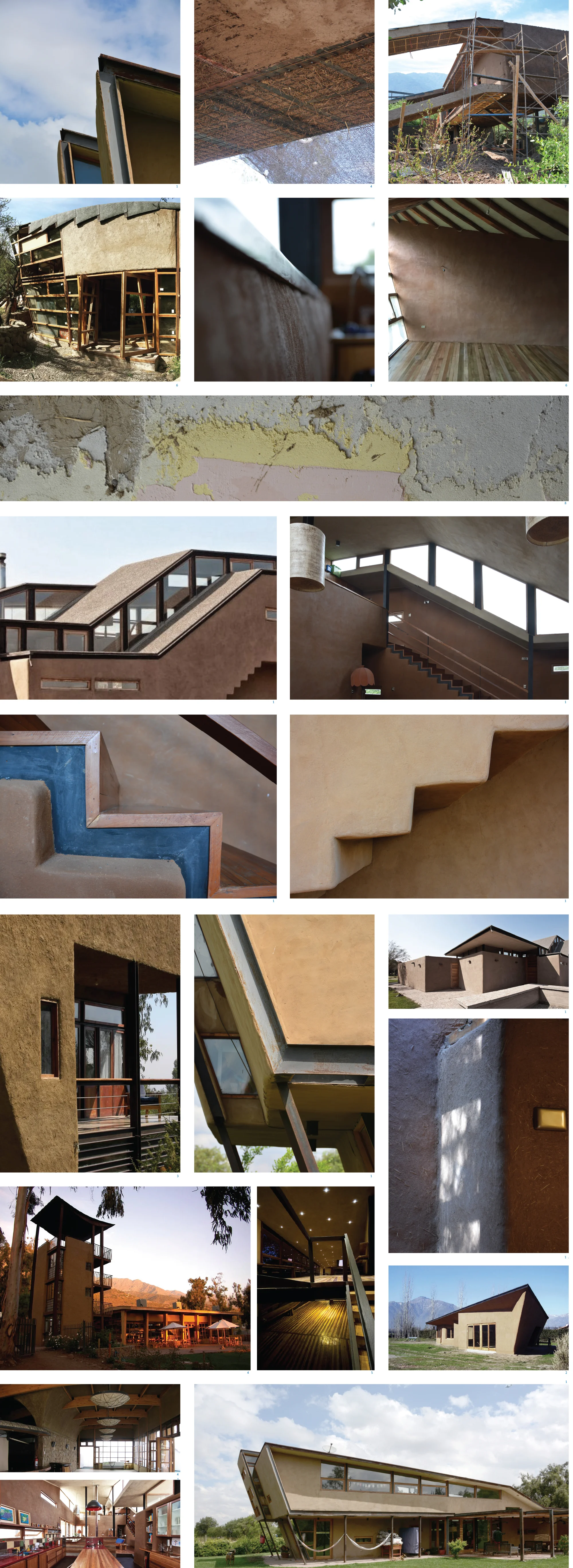
tapia
(rammed earth)
Rammed earth, called tapia in Spanish or pisé in French, is a technique in which layers of earth are compacted inside a reinforced mold. Tapia construction is an iterative process. As each section of the wall is completed the mold is disassembled and reassembled on the adjacent space until the first level of the layout is completed. The same process is repeated with the mold mounted on top of the previous level until the structure reaches it final height. Any variations in the walls shape or openings require a different mold or an insert.
Rammed earth walls are typically 40-150 cm thick, depending on the height of the structure. Traditionally, the compaction is performed by 1-3 pisoneros with wooden tampers, but modern builders often employ gas and pneumatic powered compactors. In countries without the risk of earthquakes, rammed earth structures reach 8m in height without reinforcement. In seismic zones, rammed earth structures require either internal or external reinforcement.



QUINCHA or Bahareque
(wattle & daub)
In its essence, wattle and daub is a wooden structure filled with earth and organic materials (often straw). The frame of wattle and daub structures can be made of bamboo, wood or metal. Of the three principal techniques in South America, it is the most earthquake resistant and does not need to be reinforced.
Since it is lighter and relatively flexible, wattle and daub is very versatile and allows for unique shapes and cantilevering. It is often used in combination with other techniques to form partition walls, or in the case of highly seismic areas, a construction system that has tapia or adobe on the first floor and the more earthquake resistant wattle and daub on the upper floors. The disadvantage is that wood or iron can be prohibitively expensive for poor communities, especially in areas of low rainfall where wood must be transported across great distances. For similar reasons, wattle and daub can have a higher environmental impact than adobe or tapia.
The 19th century buildings in Valparaiso, Chile, are not immediately recognizable as earthen structures.
All that is visible from the outside are the colorful and graffiti-laden corrugated metal panels, recycled from the city’s vast shipping industry. If peeled away, it becomes immediately clear that Valparaiso, like so much of Latin America, is a city of raw earth. Most of the historical buildings in the city, which are protected by UNESCO, are made of Adobillo, a technique that utilizes a thick wooden frame (also recycled from the shipping industry) filled with adobe blocks. They are truly local structures, built entirely from locally available, often recycled materials.
The projects from Minga Valpo maintain the tradition of utilizing recycled materials. For example, they are using shipping pallets filled with straw and coated in earth to build homes and community centers after the fires destroyed thousands of homes in 2014.
Terra Panel
Terra panel is a patented innovation from Surtierra Arquitectura. The technique is a direct response to the high risk of earthquakes in Chile, where banks are often unwilling to fund the construction of raw earth structures. This technology allows the architect to reassure client, government and funding agency that the proposed building, which is essentially a metal structure with earthen filling, is safe and durable.
The Terra Panel construction technique consists of light gauge rebar welded into a grid formation and mechanically folded to form 45 degree angles (with 5 vertical pieces corresponding to each oscillation), horizontal oscillations along the length of the panel. The grid structure serves to contain the earthen filling, which consists of wetted earth and organic matter (typically straw). The panel can contain walls with two densities: 750 kg/m3 and 1800 kg/m3. The goal is to have walls that interact with the environment differently, for example, the heavier walls should be oriented toward the sun (the North in the Southern Hemisphere) so as to maximize the thermal transfer and insulations.
Terra panel is a versatile technique that can support multiple floor structures, as well as be used for ceilings. The technology has a high potential for commercialization, which can bring economies of scale that are not available to all techniques. With 10 years of usage in Chile, the final result of the terra panel is an extremely versatile and malleable sustainable technology which adapts to the threat of earthquake.
Supporting material was created for the exhibition on July 2017 at Cornell NYC
Mixed techniques over canvas 24"x18" each
Exhibition at Cornell NYC Studio
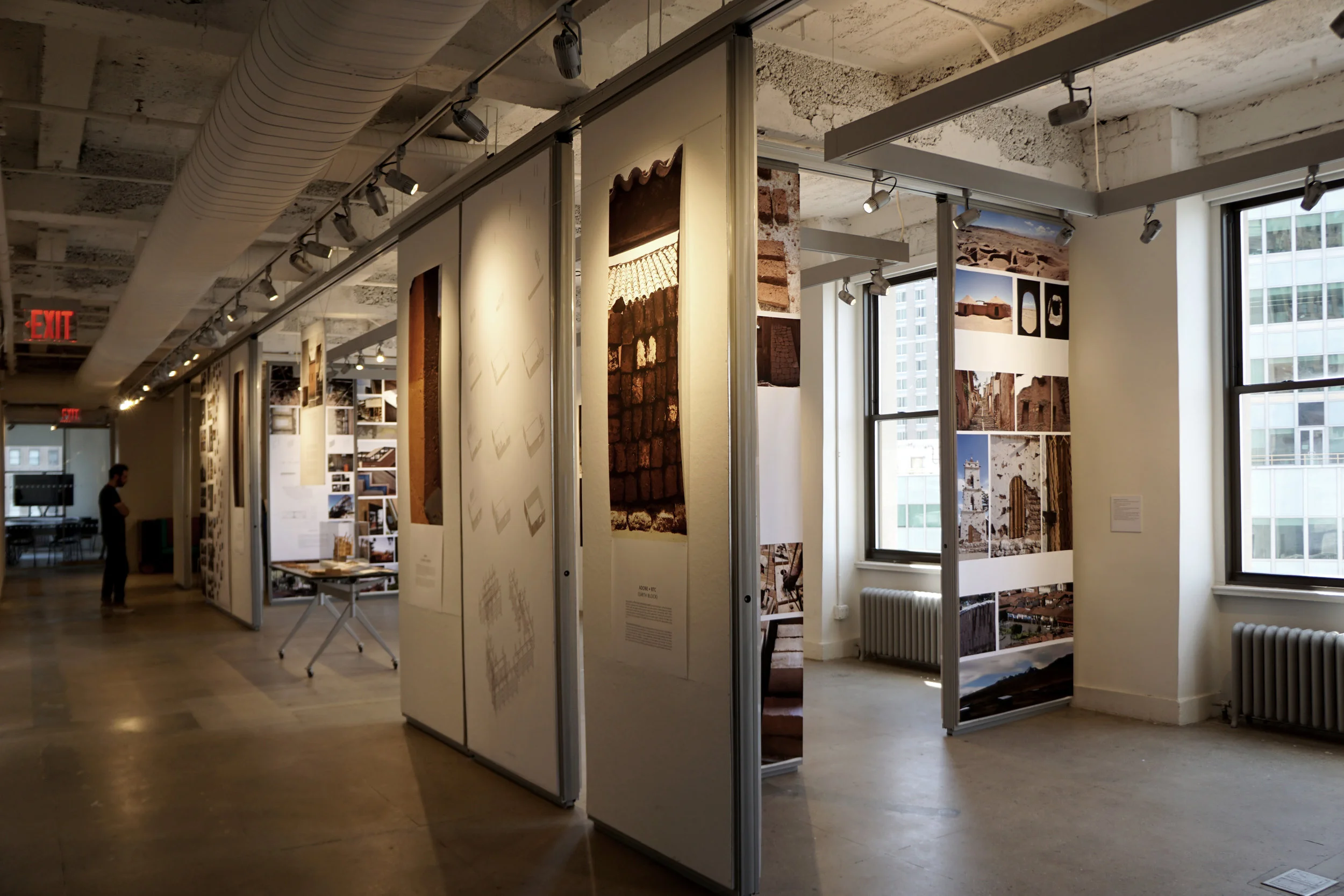

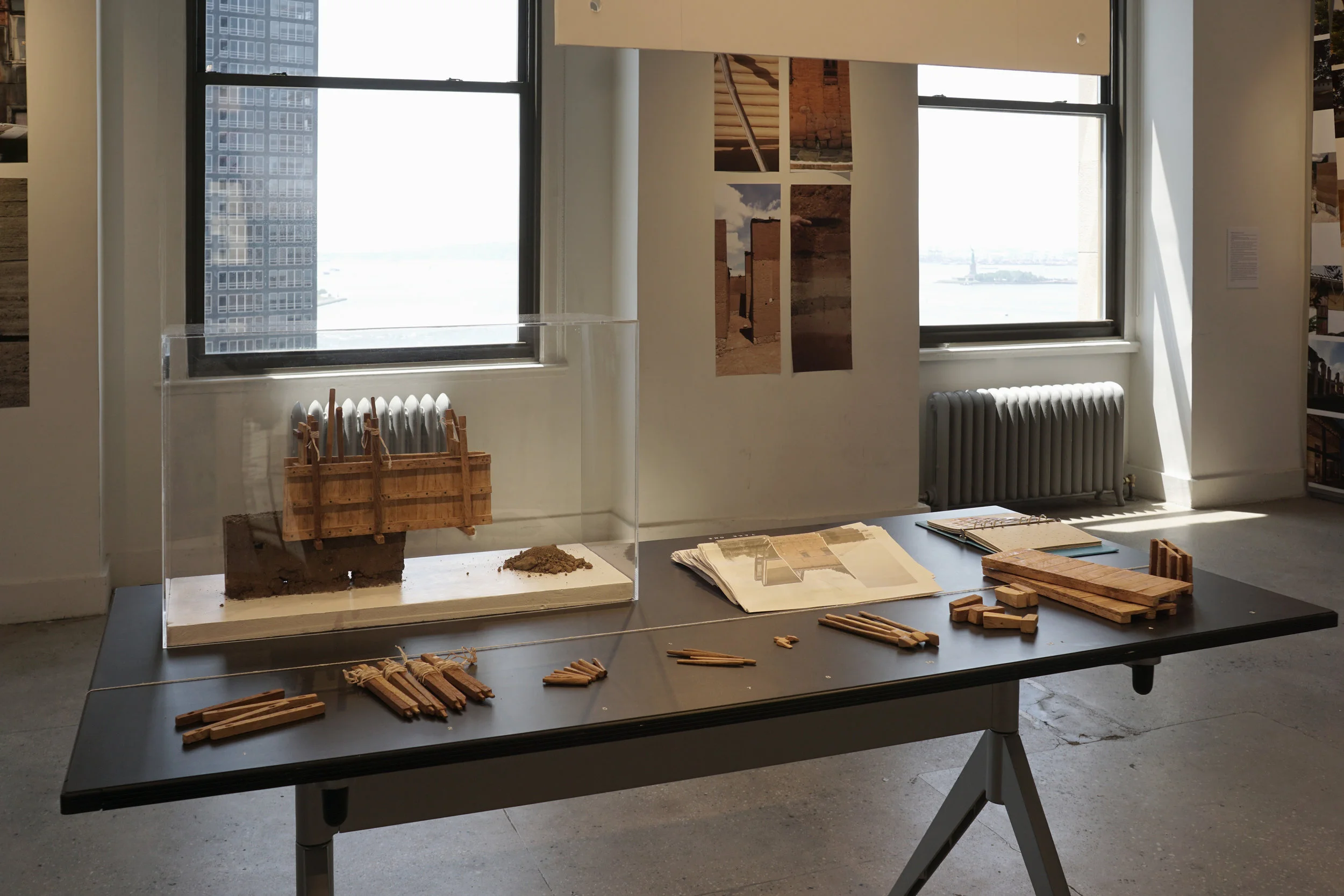

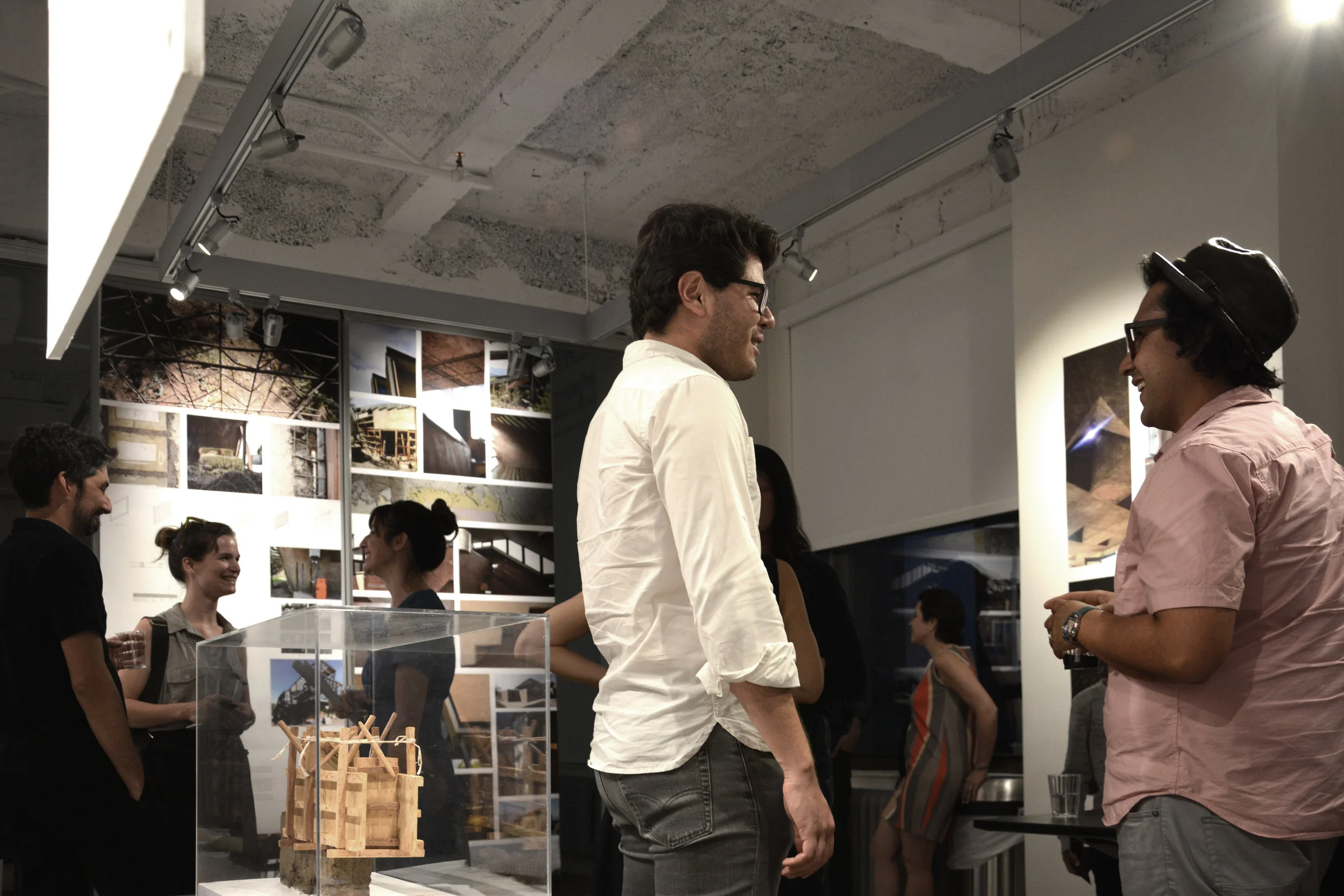
Casa Munita. Batuco, Chile 2011. Designed by Surtierra Arquitectura
Casa Pirque. Pirque Chile 2007. Designed By Surtierra Arquitectura. Photos courtesy of Surtierra Arquitectura.
3. Casa Peñaloven, Chile. Designed by Marcelo Cortés. Santiago de Chile. Photo from website.
4. Granja Aventura, Chile. Designed by Marcelo Cortés. Santiago de Chile 2011. Photo from website.
5. Centro de Ecologia Aplicada, Santiago de Chile. Designed by Marcelo Cortes.
6. Officina Surtierra Peñalolén. Santiago de Chile 2016. Designed By Surtierra Arquitectura.
7. Casa Mario Alvarez, Santiago de Chile Under Construction. Designed by Surtierra Arquitectura.
8. Plaster finish, refined in sifted decorative clays. By Surtierra Arquitectura
9. Valparaiso city and 19th Century Construction techniques.
10. Reconstruction work of Minga Valpo. Valparaiso, Chile. Photos courtesy of Minga Valpo.
11. Ludoteca, Center for children exhibition. Santiago de chile. “Villa Solar Exhibition” funded by Construye Solar Social Sustainable Design. Photos courtesy of Minga Valpo.
12. Mrs Esmera House. Valparaiso, Chile 2014. By Minga Valpo.
13. Ludoteca, Center for children. Valparaiso, CHile 2016. By Minga Valpo.
14. Riveros Family Dry Bathroom. Valparaiso, Chile 2015. Photo from website.